NEW

QUESTIONS ARE ..VERY OFTEN INDUCTED NORMALLY ………..
when ever time spare me now a days 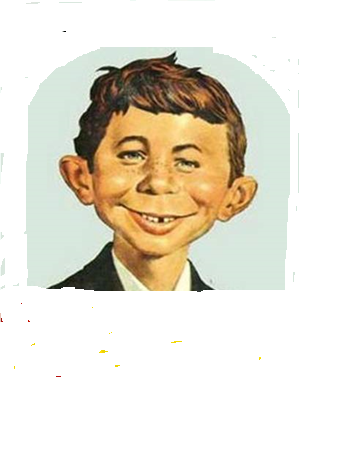
PREVIOUS QUESTIONS FROM 0001 TO TILL 0238 TODAY 18AUG 2025) CAN BE PROVIDE TO INDIVIDUAL,s ONLY BY THERE TELEPHONIC call
REQUEST 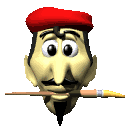
MY MOBILE NUMBER IS 92 3232500934
Question of the DAY for (AIRFRAME) 0239
Q In which direction does the aileron control the aircraft’s movement?
1 Roll.
2 Pitch.
3 Yaw.
4 Climb.
XXXXXXXXXXXXXXXXXXXXXXXXXXXXXXXXXXXXXXXXXXXXXXXXXXXXXXXXXX
Question of the DAY for (AIRFRAME) 0240
Q . A helicopter’s ability to maintain a steady hover is influenced by:
1 The airspeed of the helicopter.
2 The altitude of the helicopter.
3 The power settings and balance of the helicopter.
4 The direction of the helicopter’s flight path.
CORRECT ANSWER IS
3.The power settings and balance of the helicopter.
EXPLANATION
A helicopter’s ability to maintain a steady hover is influenced by the power settings (torque and collective pitch) and balance (center of gravity and weight distribution). This is because hovering requires precise control over the rotor’s angle of attack and thrust to counteract the weight and any external factors like wind.
The other options are not directly relevant to maintaining a steady hover:
- Airspeed is more relevant to forward flight, as a helicopter’s airspeed is typically zero when hovering.
- Altitude can affect the helicopter’s performance due to changes in air density, but it’s not the primary factor in maintaining a steady hover.
- Direction of the helicopter’s flight path isn’t relevant to hovering, as the helicopter is stationary relative to the ground.
XXXXXXXXXXXXXXXXXXXXXXXXXXXXXXXXXXXXXXXXXXXXXXXXXXX
Question of the DAY for (AIRFRAME) 0241
Q ////?????
CORRECT ANSWER IS
XXXXXXXXXXXXXXXXXXXXXXXXX
Question of the DAY for (AIRFRAME)0242
Q. ???????????????
CORRECT ANSWER IS :
EXPLANATION
ITS SO CLEAR NOW 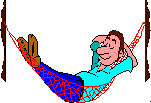
XXXXXXXXXXXXXXXXXXXXXXXXXXXXXXXXXXXXXXXXXXXXXXXXXXXXXXXXXXXXXXXXXXXXXXXXX
Question of the DAY for (AIRFRAME) 0243
Q “?????????????????? 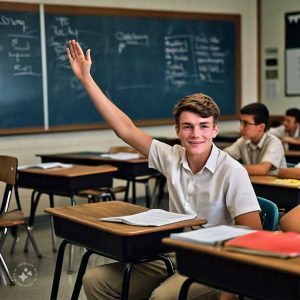
EXPLANATION
-
XXXXXXXXXXXXXXXXXXXXXXXXXXXXXXXXXXXXXXXXXXX
Question of the DAY for (AIRFRAME) 0244
Q ????????????????????
CORRECT ANSWER IS
EXPLANATION
-
XXXXXXXXXXXXXXXXXXXXXXXXXXXXXXXXXXXXXXXXXXXXXXXXXXX
Question of the DAY for (AIRFRAME) 0245
Q. ?????????????????????
CORRECT ANSWER IS
IT IS SO CLEAR NOW 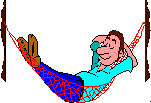
XXXXXXXXXXXXXXXXXXXXXXXXXXXXXXXXXXXXXXXXXXXXXXXXXXXXXXXXXX
Question of the DAY for (AIRFRAME) 0246
Q. ???????????????
.
CORRECT ANSWER IS
EXPLANATION
XXXXXXXXXXXXXXXXXXXXXXXXXXXXXXXXXXXXXXXXXXXXXXXXXXXXXXXXXXXXXXXXXXXXXXXXXXXXXXXXXXXXXXX
Question of the DAY for (AIRFRAME) 0247
Q. ????????????????????????
CORRECT ANSWER IS
Explanation:
XXXXXXXXXXXXXXXXXXXXXXXXXXXXXXXXXXXXXXXXXXXXXXXXXXXXXXXXXXXXXXXXXXXXXXXX
THESE ANSWERS ARE
RESEARCHED ANSWERS
and MOSTLY EXPLAINED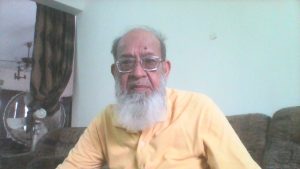
FOR A STUDENT SEARCHING FOR KNOWLEDGE UPDATE
THE SOONER I GET THROUGH THE AIRFRAME QUESTION & THE RIGHT ANSWER WITH EXPLANATIONS WILL START THE POWER PLANT QUESTION AND RIGHT ANSWER WITH THE EXPLANATIONS
FOR EXAMPLE, SAMPLE QUESTION AND ANSWER COMING SHORTLY
When a propeller on a reciprocating engine strikes an object causing the engine to suddenly stop, what should be done to the engine?
- Perform a power check to determine internal damage.
- Check the fuel screens for metal deposits.
- Perform a compression check.
- Check the crankshaft for distortion.
CORRECT ANSWER IS
4.Check the crankshaft for distortion.
EXPLANATION
When a propeller strikes an object and causes the engine to suddenly stop, it can cause a sudden shock load on the crankshaft. This can lead to internal engine damage, including crankshaft distortion or bending.
Checking the crankshaft for distortion is critical because:
-
A bent or distorted crankshaft can cause catastrophic engine failure if the engine is restarted.
-
A visual inspection of the crankshaft may not reveal any damage, so a detailed check using specialized tools is necessary.
The other options are incorrect:
-
Option 1: A power check may not reveal internal damage caused by the sudden stop.
-
Option 2: Checking fuel screens for metal deposits may indicate other issues, but it’s not directly related to the sudden engine stop.
-
Option 3: A compression check can indicate engine problems, but it may not specifically reveal crankshaft distortion.
MY email anmfahm@gmail.